De metamorfose van een onderhoudsdienst
From reaVan reactief naar gepland onderhoud
“Ik vind het echt jammer dat ik al niet veel eerder in zo’n werkplaats heb mogen werken.” Aan het woord is één van de E&I monteurs in de Vynova vestiging in Beek (NL). Recent heeft hij samen met zijn collega’s de werkplaats georganiseerd volgens de 5S methode. Hij is trots dat dit de referentie is voor zijn collega’s die elk hun werkplaats op dezelfde manier aanpakken. Dit is slechts één van de vele veranderingen die in de voorbije 12 maanden door de medewerkers zijn gerealiseerd, tot hun eigen grote tevredenheid.
Ik ben op bezoek bij mijn Stork collega Ron Bezoen die hier sinds ruim 2 jaar de organisatie begeleidt bij de realisatie van een ware metamorfose van de onderhoudsorganisatie. Het is opmerkelijk wat de mensen van Vynova Beek onder zijn begeleiding hebben gerealiseerd sinds mijn vorige bezoek, nu 12 maanden geleden.
Het reservedelenmagazijn komt mij over als echt netjes en ordelijk. De magazijnbeheerder vertelt trots dat hij nu nog maar zelden wordt aangesproken omdat monteurs de nodige artikels niet kunnen vinden. Doch de magazijnbeheerder geeft aan dat er nog een MRO onderdeel (Maintenance, Repair and Operating supplies) in het programma zit aan te komen om de magazijnwerking verder te optimaliseren.
In de koffiehoek valt mijn oog op een hele grote poster met daarop de roadmap van het hele programma. Op de verschillende verbeterassen zijn telkens de bouwstenen in volgorde van realisatie te zien. Met kleuren is de vordering aangegeven. Ik kan me voorstellen dat dit iedereen, van ver of dichtbij betrokken, dagelijks herinnert aan het belang van het verbeterprogramma. Iemand laat zich ontvallen: ”Zonder dit Asset Management programma zou ons bedrijf wellicht in moeilijk vaarwater terechtkomen.”
Duidelijke rolverdelingen
Ik ontmoet de werkvoorbereider en de maintenance engineer. Ze delen eenzelfde bureelruimte. Dit is niet toevallig, maar het resultaat van een bewuste keuze. Het faciliteert het spontaan uitwisselen van gegevens en het steeds beter samenwerken. Een fundamentele verbetering was het helder definiëren van de werkstroom. Daarbij is duidelijk afgesproken wie welke rol hierin neemt. Zo zijn er nu werkvoorbereiders, een planner en een maintenance engineer, die precies weten wat van hen verwacht wordt, en die daardoor ook beter kunnen samenwerken. Dit resulteerde in veel meer focus bij elke speler waardoor elkeen ook in staat is om steeds beter te worden in wat hij doet.
Ron: “Monteurs hebben het idee dat er voor hen heel weinig is veranderd. Dat is voor mij een indicatie dat de veranderingen voor hen blijkbaar heel soepel zijn verlopen. Want het leven van de monteurs en de werkplaatsleider ziet er wel degelijk heel anders uit dan een jaar geleden.” Ron gaat verder: “Toen besteedden ze nog 80% van hun tijd aan het verhelpen van storingen. Als er nog wat tijd restte, deden ze ook wel eens een preventieve actie. Nu is 80% van het werk dat ze doen voorbereid en in een planning vastgelegd.
Eerst verzamelen de werkvoorbereiders per werkorder alles wat monteurs nodig hebben om het werk veilig, kwalitatief en efficiënt uit te voeren. Ze bepalen hierbij onder meer welke onderdelen nodig zijn, bekijken of deze voorradig zijn en bestellen ze indien nodig. De planner neemt de werkopdrachten in de planning op van zodra alle nodige onderdelen beschikbaar zijn. Een week voor de geplande uitvoering verzamelt de magazijnbeheerder de onderdelen per werkorder in zogenaamde kits. De week voor de uitvoering wordt het geplande werk ook met de monteurs doorgesproken. De monteurs controleren daarop per werkorder de klaargelegde onderdelenkits. Dit alles zorgt ervoor dat zij elke dag opnieuw het geplande werk zonder tijdverlies kunnen aanvatten en afwerken. De eerste prioriteit voor de monteurs en de werkplaatsleider is om het werk volgens de planning te realiseren. De werkplaatsleider neemt het initiatief om contractor medewerkers in te zetten als de capaciteit aan eigen monteurs niet toereikend is. Het niet-planbare storingsonderhoud wordt opgepakt door een paar hieraan toegewezen monteurs. Dit alles maakt dat de meeste monteurs nog maar zelden in hun werkzaamheden worden onderbroken omwille van dringend storingsonderhoud.”
Het CMMS is geoptimaliseerd
Ik merk op dat de hele werking op dit moment zeer vanzelfsprekend lijkt. Ron: “Vergis je niet! We hebben in de voorbije paar jaar echt niet stil gezeten. Er is echt veel werk verzet door de organisatie om zover te komen. Medewerkers die de actuele toestand van de installatie goed kennen hebben de boomstructuur na 10 jaar opnieuw geactualiseerd. Hierdoor kunnen nu alle meldingen (werkaanvragen) aan de juiste TAG gelinkt worden, en wordt hierdoor ook een correcte historiek van onderhoud opgebouwd. Productie, procesingenieur en onderhoud hebben samen de kriticaliteit bepaald van alle installatiedelen. Deze informatie is in het CMMS (Computerized Maintenance Management System – Asset management software) beschikbaar en wordt door de operatoren gebruikt bij het bepalen van de prioriteit van de werkaanvragen die ze aanmaken. Alle operatoren zijn hiervoor opgeleid en worden regelmatig bijgestuurd waar de kwaliteit van de meldingen nog niet voldoet. In de dagelijkse ochtendvergadering worden nieuwe aanvragen gezamenlijk bekeken. Aanvragen die onvolledig of onduidelijk zijn gaan terug naar de melder. De aangegeven prioriteit wordt geverifieerd, en hoeft nog slechts voor 10% aangepast te worden. Het is nu ook in het CMMS voorzien dat aanvragen kunnen geschrapt worden als daar redenen voor zijn. Dit kon vroeger eenvoudigweg niet. Uiteraard wordt de melder hierover steeds geïnformeerd – met de nodige argumenten erbij.”
“Het CMMS (SAP-PM) is ook op verschillende punten aangepast om de nieuwe manier van werken goed te ondersteunen. Werkvoorbereiders, planner en maintenance engineer zijn stuk voor stuk in hun nieuwe rol opgeleid en gecoacht geweest. En waar we nu staan, is geen eindpunt. We blijven verder verbeteren. Op het vlak van werkvoorbereiding en planning hebben we een verbeterloop ingericht waarbij de werkplaatsleider en de monteurs een belangrijke rol hebben. We verwachten dat zij terugkoppelen op welke punten zowel de werkvoorbereiding als de planning nog verder kunnen verbeteren. De planner werkt nu met een horizon van 2 weken, maar we staan klaar om te gaan plannen met een horizon van 13 weken. Er is nu ook een lijst met niet-dringend opvulwerk. Hierdoor is leegloop bij de monteurs voltooid verleden tijd geworden.”
Een verbeterde betrouwbaarheid
De reliability engineer, aangeworven 2 jaar geleden, komt erbij. “De voorbije maanden zien we een duidelijke dalende trend van het aantal uren stilstand per maand . We hebben er vertrouwen in dat we de doelstelling die we ons hebben gesteld binnen de voorziene tijd gaan halen. Nochtans zijn we hier nog maar aan het begin. We hebben het bestaande onderhoudsplan volledig getoetst aan de hand van de FMEA methodiek (Failure Mode and Effect Analysis). Alle gekende faalrisico’s en de daarbij horende mitigerende maatregelen zijn nu centraal gedocumenteerd. Een reeks verbeteringen is intussen in het bestaande onderhoudsplan aangebracht en hiaten zijn opgevuld. Maar nog belangrijker is dat we er nu ook steeds meer in slagen het onderhoudsplan ook daadwerkelijk en stipt uit te voeren. We zijn er nog niet helemaal, maar we worden hierin steeds beter.”
Ron gaat verder: “We hebben intussen ook de eerste stappen gezet in het stelselmatig verbeteren van de betrouwbaarheid door te leren uit storingen. Dit vereist dat monteurs na elke storing goed, en liefst op een gestructureerde manier, rapporteren. Daartoe zijn per type van uitrusting zogenaamde SORA codes bepaald. Die worden gebruikt om in het CMMS voor elke storing Symptoom, Oorzaak, Remedie en Actie te classificeren. Sowieso merk ik ook dat men – ook in productie – steeds meer de reflex heeft om na elke verstoring van de productie te kijken naar de onderliggende oorzaak. Dit gaat ons straks helpen om zeer gericht maatregelen te nemen om storingen te voorkomen, onder meer door het onderhoudsplan stelselmatig te verbeteren. We hanteren sinds kort ook een gestructureerde Root Cause Analyse methode om de oorzaken te achterhalen van de wat complexere storingen met grote impact. Hierbij worden verschillende disciplines betrokken, waaronder ook monteurs, zodat geen enkele invalshoek over het hoofd gezien wordt.”
De plantmanager: "Het is een team-effort"
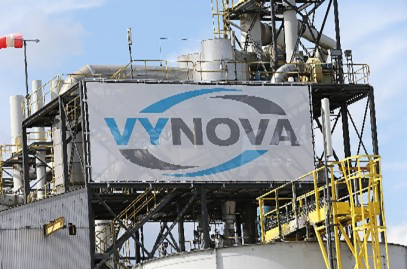
We nemen nog even de tijd voor een koffie en de plantmanager begroet ons. “Dit programma was echt een team-effort. Het heeft ons als team ook sterker gemaakt. Tijdens de eerste COVID-golf hadden we een stagnatie, misschien zelfs een terugval. Maar het was opmerkelijk hoe we door gezamenlijke focus binnen de 2 weken de terugval hadden weggewerkt en volgende stappen aan het zetten waren.
Voor mij als budgetverantwoordelijke is het een grote verbetering dat we nu de onderhoudskosten in detail budgetteren en opvolgen. Dit zorgt ervoor dat de kosten ook beter voorspelbaar zijn, we hebben minder verrassingen. Ik merk ook dat we beslissingen veel meer risk-based maken. We zijn ons veel meer bewust van de risico’s die we nemen als we deze of gene beslissing nemen.”
We nemen afscheid en ik spreek de wens uit om over een jaar nog eens terug te komen. “Dat zou fijn zijn. En ik heb er vertrouwen in dat we super trots zullen zijn op wat we dan zullen hebben bereikt.”